Case studies
sample of Precision welding for molds.
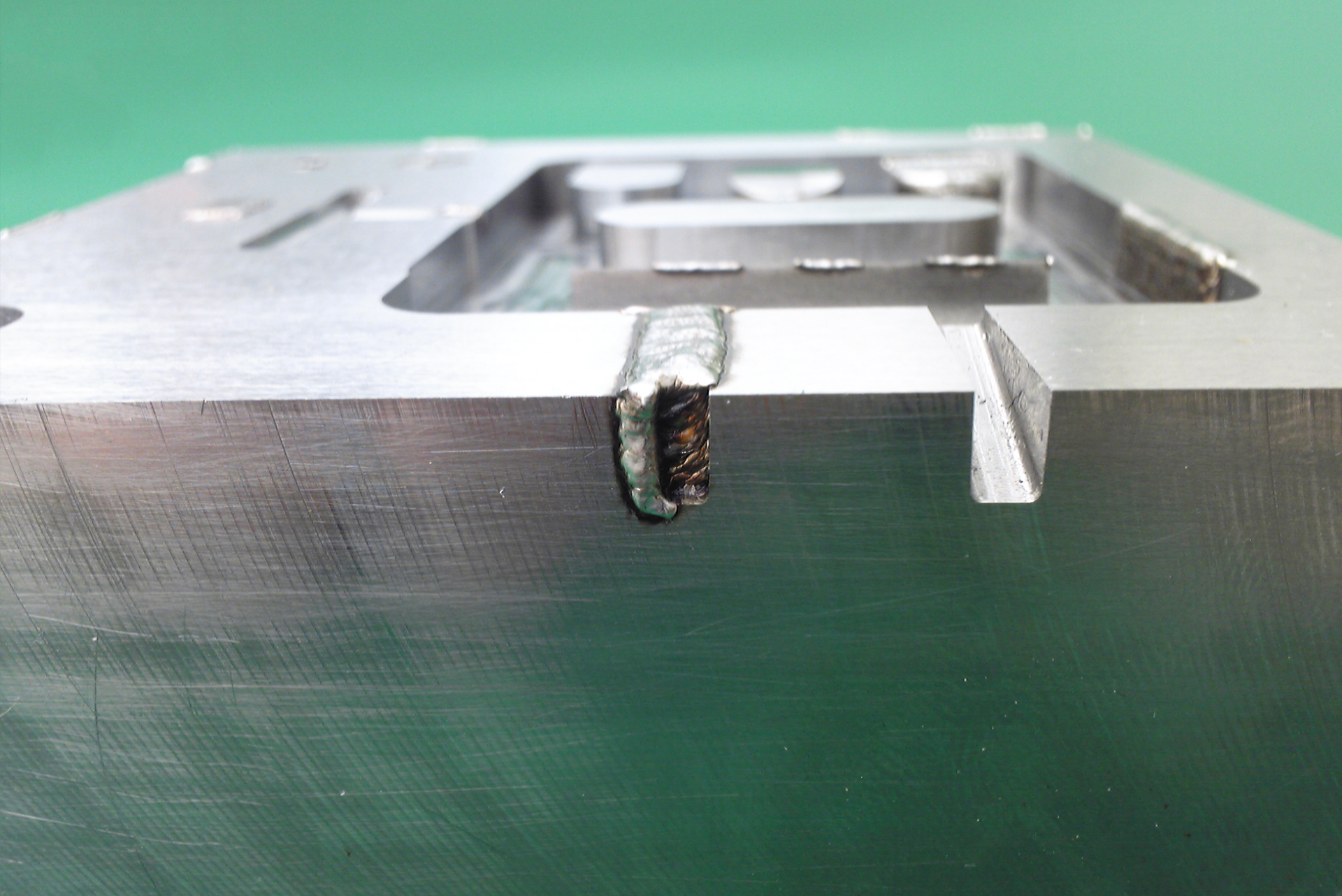
High-precision welding in a rib configuration.
Padding is welded on in order to reconfigure a rib section. Re-cutting is required and as a result the technician needs to weld without bubbling, marking or cracking.